HOME > Business
BUSINESS DESCRIPTIONBUSINESS DESCRIPTION
Infinite possibilities for manufacturing
One-stop integrated production systemIntegrated production
We support customers on various stages from mold design, manufacturing, and maintenance to supply of spare parts.
We manage mold supply system to connect Japan with other Asian countries.
MATSUOKA
GROUP
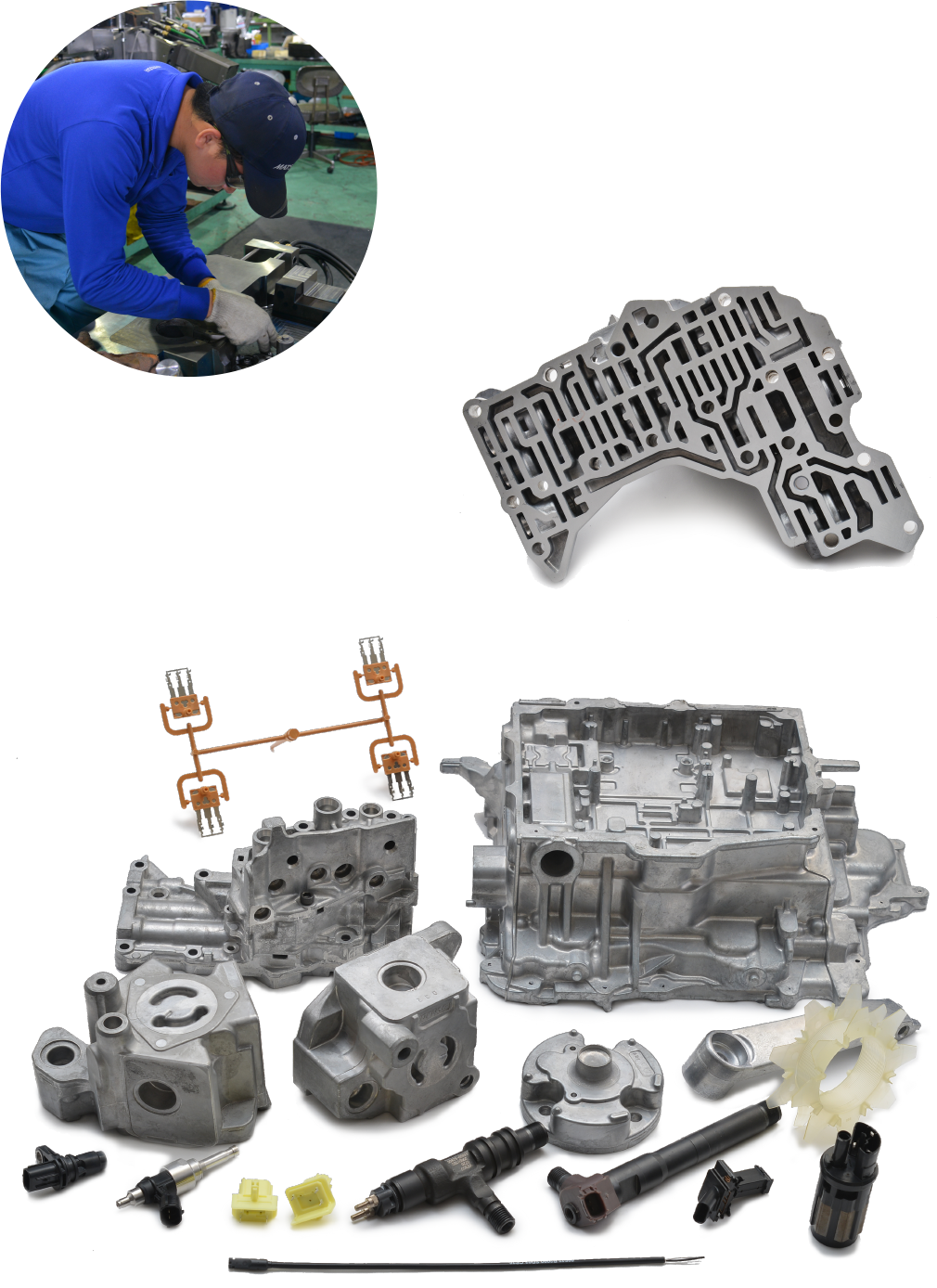
Workflow
Mainly focusing on high vacuum die casting mold and precise plastic mold, we cater to the needs with our integrated setup, from manufacturing to maintenance.We can also respond to the global needs mainly in the Asian region through Family Company Collaborationies.Please feel free to contact us for our customer-oriented service even for an order of just one piece of parts or mold repair.
Design
We create the data of customized products which support customers’ brand.
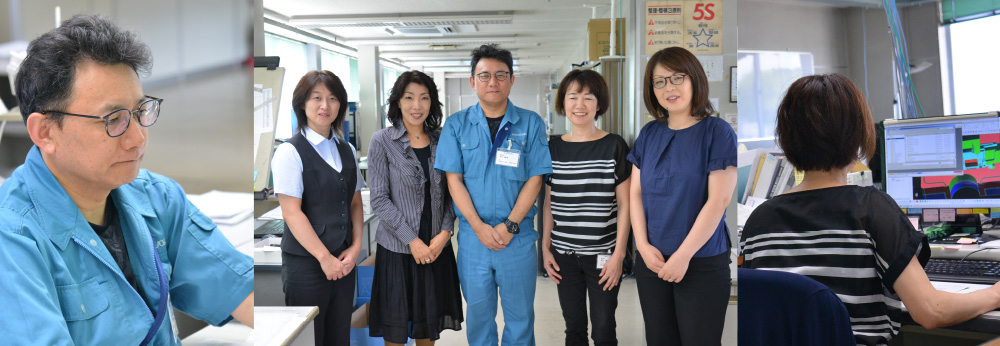
For customers requiring extra high quality and high -function for molds, we convert all designs into 3D and 2D drawings in consideration of parts manufacturing, procurement, maintenance and customers’ convenience of their global operations.
Based on information onf characteristics of customer’s products and mold specification and the status of manufacturing machines, we quantify the specification of the customized product by focusing on tolerance design with a unit of μm according to the application of the mold. In addition, we contribute to clientcustomers’ productivity improvement, per-piece cost reduction and F-IoT, by providing special joint technology realized through collaboration with other industries, additive manufacturing technique and automated design customizing system for cooling circuit as well as utilizing various analytic technology.
Production control / manufacturing
Combined strength of our technologies, know-how and network allows us to realize μm level accuracy, and reduction in lead time and cost.
It is essential for customers to promptly launch production upon quickly procuring molds required for each product in order to keep winning in the global competition.
With the aim of realizing μm accuracy, short time delivery and cost efficiency, we have built a production management system in which we make partner companies specialize in investment and roles, and share control information on equipment accuracy, inspection assurance standards and load status with them.Furthermore, we support customers to enhance their competitiveness by developing this system globally.
Processing technology
High vacuum die casting mold
Mating accuracy of 10μm level and adjustment under temperature change in mold are vital for the quality of high vacuum die casting mold.Our molds with a vacuum degree of 4kPa or less help improve the quality of the internal structure of customers’ die casting products.
Variable Valve Timing System
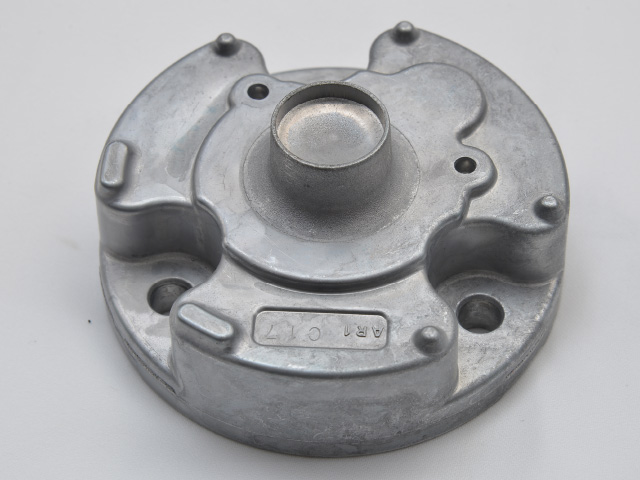
Fuel Injection System
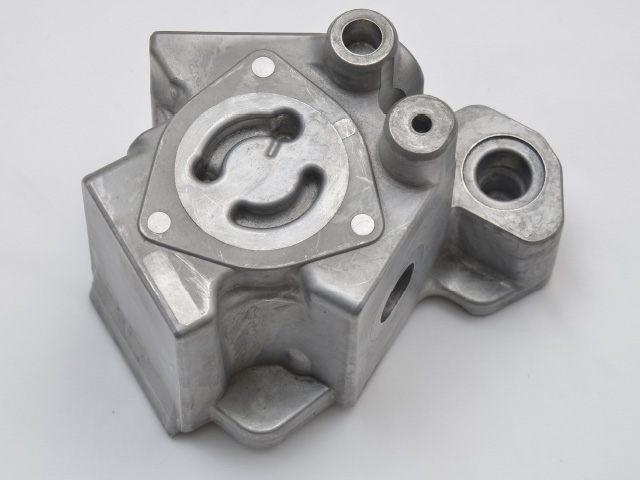
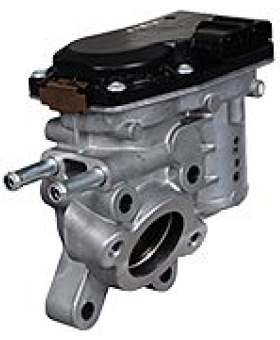
EGR valve
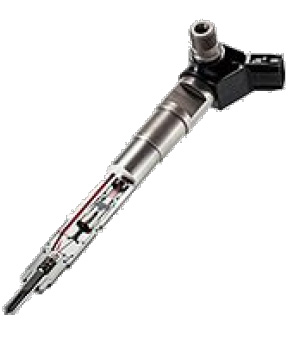
Injector
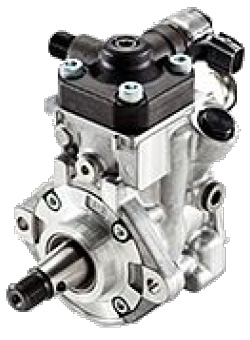
Supply pump
Highly functional plastic mold
Highly complex and advanced functional molds are required for customers who continuously aim to develop high quality and high function products and establish innovative process.Our highly functional plastic molds with a gap of 5μm or less and optimal mating face adjustment do not generate even a fine burr, contributing to customers’ stable production and improvement in their operation ratio.
Large-sized die casting mold
Our quality management technology does not allow the return of huge parts and ensures the quality required for large-sized die casting mold.Inspection assurance between processes and communication is indispensable.With various experiences and know-how, we can provide large-sized die casting molds to customers with a short delivery time.
Parts inspection
To provide “Safety” to customers and final process
We use processes including cutting work, electrical machining and grinding work, while procuring finished parts.
Inspectors ensure the role provide the completion of parts with a focus on the function of mold, fully understanding the role of each part.To achieve this,they need to communicate with the design department and finishing department.
Inspectors judge whether the parts are qualified or not based on a strict accuracy by 0.1μm on behalf of customers and final process workers.They are authorized to instruct each process to handle findings, if necessary, assuring the high quality for customers.
Finishing / Assembly / Shipping inspection
The final process completes molds as customers’ strategic tools.
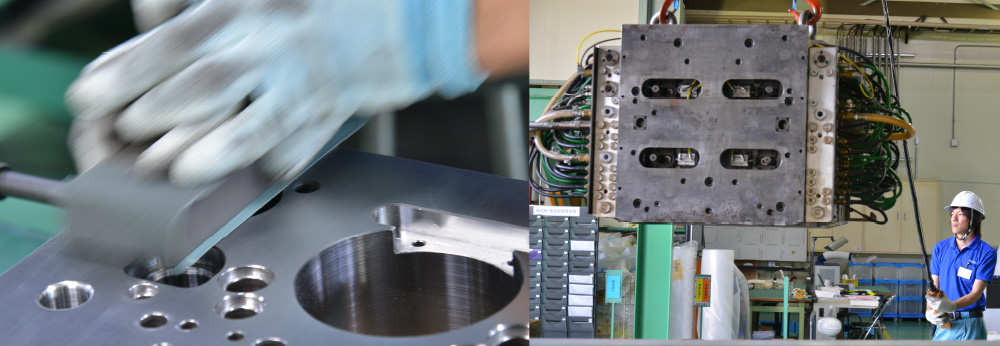
Mold, which consists of more than 100 metal processing parts, requires, careful handling.
When 10 pieces of the part manufactured with an accuracy of 2 to 5μm are lined up, their collective assembly accuracy becomes 20 to 50μm.Nevertheless, some customers require assembly accuracy of 3μm or less for molds when they are assembledy.
It depends on know-how of the finishing department whether or not to realize intent of designers and requirements from customers. The finishing department makes decisions such as “which parts should be adjusted by what amount of μm” and “what level of strength should be secured for a mating face to support a pressure of 800kgf/cm²”.
They sometimes express their opinions on behalf customers at internal meetings, and at other times they set up our molds at customers’ factories to guarantee the completeness.
This is the reason why we have strengthened “the finishing” as one of the most important process.
Maintenance
Mold maintenance as the key point to maintain operation ratio and per-piece cost control at customers.
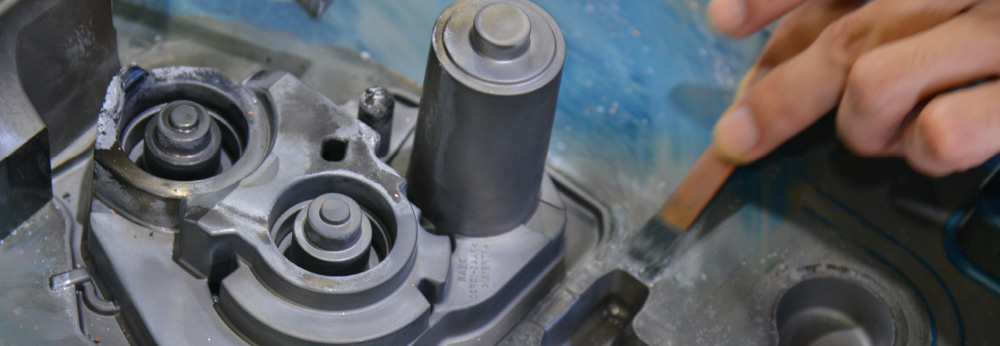
Mold maintenance is important and it includes cleaning, service life control of consumable parts, and recovery of shapes by welding and machining, requiring great care and expertise.The finishing department, which handles mold maintenance, provides feedback on aspect of design such as improvement in materials to maintain accuracy and maintainability, as well as improvement in surface treatment for longer shelf lives.
SERVICE
AZUKI (THAILAND)Mold maintenance
From mold maintenance, which is crucial for customers to maintain their factory operating ratio, to supply of spare parts, AZUKI provides customer support for mold, catering for customers’ needs in the Asian region in cooperation with the Japanese bases.
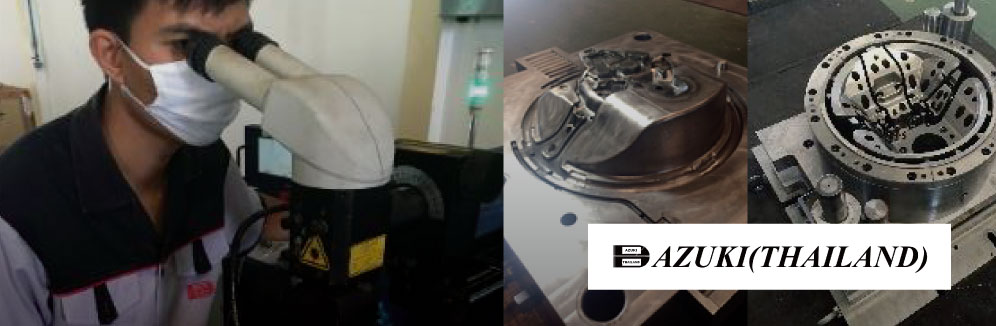
AZUKI (THAILAND), a joint venture established with two Japanese Family Companies, started its operation in 2012 with the aim of providing customer supports in the Asian region.Its operation includes maintenance of die casting, plastic and press molds, supply of spare parts and mold dimension adjustment.
We have strengthened techniques at AZUKI for argon/laser welding, machining and finishing works particularly for maintenance of die casting molds to meet the needs for correction of cracks, recovery of damaged shapes, and readjustment of mating portion levels.
With its improvement culture developed, AZUKI have gained a high reputation from various customers. Its local staff member can respond to customers with technical discussions, leveraged by its know-how acquired to satisfy the needs of Japanese makers.AZUKI is now the Southeast Asian base to support global supply of molds in collaboration with overseas Family Companies.
Contactお問い合わせ
For inquiries about products and services, please contact us using the inquiry form.
Click here for inquiries, quotations and consultations.
NAGOYA052-621-2136
GUNMA0276-73-2563